State-of-the-art technology in plastic extrusion for innovative industries
State-of-the-art technology in plastic extrusion for innovative industries
Blog Article
A Comprehensive Overview to the Process and Benefits of Plastic Extrusion
In the vast realm of production, plastic extrusion arises as a necessary and highly effective procedure. Transmuting raw plastic right into continual profiles, it provides to a wide variety of markets with its impressive flexibility.
Comprehending the Fundamentals of Plastic Extrusion
While it may show up facility at initial glimpse, the process of plastic extrusion is essentially basic. The process begins with the feeding of plastic product, in the kind of powders, pellets, or granules, into a warmed barrel. The designed plastic is then cooled, strengthened, and reduced into desired sizes, finishing the procedure.
The Technical Process of Plastic Extrusion Explained

Sorts Of Plastic Suitable for Extrusion
The option of the appropriate sort of plastic is a vital element of the extrusion process. Different plastics offer special residential or commercial properties, making them a lot more suited to certain applications. Polyethylene, for instance, is typically used because of its low expense and easy formability. It offers outstanding resistance to chemicals and dampness, making it perfect for products like tubes and containers. Polypropylene is another preferred selection due to its high melting factor and resistance to exhaustion. For more durable applications, polystyrene and PVC (polyvinyl chloride) are commonly picked for their toughness and sturdiness. Although these are typical options, the option eventually depends on the certain demands of the product being produced. So, understanding these plastic types can dramatically improve the extrusion procedure.
Contrasting Plastic Extrusion to Various Other Plastic Forming Approaches
Understanding the kinds of plastic appropriate for extrusion leads the way for a more comprehensive conversation on how plastic extrusion piles up versus various other plastic forming techniques. These include shot molding, strike molding, and thermoforming. Each technique has its one-of-a-kind usages and benefits. Injection molding, as an example, is excellent for developing complex components, while blow molding is best for hollow items like containers. Thermoforming excels at developing big or superficial parts. Plastic extrusion is exceptional when it comes to creating constant profiles, such as pipelines, gaskets, and seals. It likewise permits a regular cross-section along the length of the product. Hence, the choice of approach mainly depends upon the end-product requirements and requirements.
Secret Advantages of Plastic Extrusion in Production
In the world of production, plastic extrusion provides lots of substantial advantages. One you can try here significant advantage is the cost-effectiveness of the process, that makes it a financially enticing production method. Furthermore, this method provides superior item adaptability and enhanced production rate, thus raising general manufacturing effectiveness.
Affordable Production Approach
Plastic extrusion leaps to the center as learn this here now a cost-effective manufacturing approach in manufacturing. This procedure attracts attention for its ability to produce high volumes of material rapidly and effectively, offering suppliers with significant savings. The main price advantage is the capacity to make use of much less expensive basic materials. Extrusion makes use of thermoplastic products, which are much less expensive contrasted to porcelains or steels. Better, the extrusion process itself is reasonably straightforward, minimizing labor costs. In addition, plastic extrusion calls for less power than typical manufacturing approaches, adding to reduced operational costs. The procedure also minimizes waste, as any excess or defective materials can be recycled and recycled, giving one more layer of cost-effectiveness. On the whole, the economic advantages make plastic extrusion a highly appealing alternative in why not try these out the manufacturing sector.
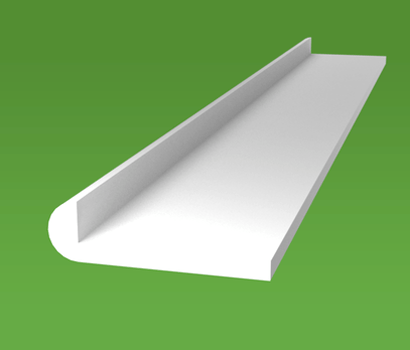
Superior Item Versatility
Beyond the cost-effectiveness of plastic extrusion, another substantial benefit in producing lies in its premium item versatility. This makes plastic extrusion an optimal option for markets that need personalized plastic components, such as automotive, building and construction, and product packaging. In essence, plastic extrusion's item versatility fosters development while enhancing operational performance.
Boosted Manufacturing Rate
A substantial benefit of plastic extrusion exists in its enhanced manufacturing speed. Few various other production processes can match the rate of plastic extrusion. Additionally, the capacity to maintain regular high-speed manufacturing without compromising product top quality sets plastic extrusion apart from other approaches.
Real-world Applications and Effects of Plastic Extrusion
In the realm of manufacturing, the strategy of plastic extrusion holds profound significance. This procedure is extensively made use of in the production of a variety of products, such as plastic tubes, window frameworks, and climate stripping. Consequently, it greatly influences sectors like construction, packaging, and vehicle sectors. Additionally, its effect reaches daily items, from plastic bags to toothbrushes and non reusable cutlery. The economic benefit of plastic extrusion, largely its high-volume and economical outcome, has transformed production. The ecological impact of plastic waste stays a problem. Therefore, the industry is persistently pursuing innovations in eco-friendly and recyclable products, showing a future where the benefits of plastic extrusion can be kept without compromising ecological sustainability.
Final thought
Finally, plastic extrusion is a reliable and extremely reliable technique of changing basic materials into diverse items. It uses various benefits over various other plastic developing approaches, including cost-effectiveness, high result, marginal waste, and design versatility. Its effect is exceptionally felt in different sectors such as building and construction, automobile, and customer products, making it a critical procedure in today's production landscape.
Delving much deeper into the technical procedure of plastic extrusion, it begins with the choice of the suitable plastic product. When cooled, the plastic is cut into the called for lengths or injury onto reels if the product is a plastic movie or sheet - plastic extrusion. Contrasting Plastic Extrusion to Various Other Plastic Forming Techniques
Comprehending the types of plastic suitable for extrusion paves the means for a more comprehensive conversation on exactly how plastic extrusion stacks up versus various other plastic creating techniques. Couple of other production procedures can match the rate of plastic extrusion.
Report this page